High-Performance Industrial Custom Furnaces & Ovens
Custom industrial furnaces and ovens are designed and manufactured to meet your application’s unique specifications. Whether you want to produce higher processing temperatures, better temperature uniformity, increased efficiency gains, or require a custom industrial furnace with the highest quality performance and reliability, Kleenair delivers the innovative design and engineering capabilities you need.
Contact us for more information regarding our custom designed and manufactured industrial furnace and ovens, or call us at 888-570-0620, and we will gladly assist you with any questions. Kleenair Products Co. is your trusted manufacturing partner for precision-manufactured industrial furnaces and ovens.
Table of Contents
Industrial Furnace & Oven Advantages
Kleenair Products Co. is the industry’s premier choice for custom industrial furnace and oven manufacturing. We have been designing, engineering, manufacturing, and installing custom industrial furnaces and ovens for over 50 years. Kleenair has the experience and the expertise to create custom furnaces and ovens that deliver the performance that our customers’ processes require. Custom industrial oven and furnace advantages include:
- Advanced Combustion Systems for Enhanced Temperature Uniformity
- Premium Quality Components
- Rugged Construction for Extended Working Life
- State-of-the-Art Features for Exceptional Usability
- Innovative, State-of-the-Art, Control Systems
Custom Industrial Furnaces & Ovens Designed to Meet Your Application Needs
Kleenair Products Co. adheres to the strictest standards for safety, productivity, efficiency, and uniformity. We provide custom furnaces, ovens, and handling systems for aerospace, military, and other demanding markets that require tight tolerances and superior performance.
- Aerospace Materials- Processing Titanium, Super Alloys, and Others
- Forging
- Heat Treating and Stress Relieving.
- Tungsten and Molybdenum Reduction
- Titanium and Zirconium Reduction / Distillation
- Powdered Metal and Sintering
- Investment Casting
- Quenching Systems
Custom Industrial Furnace & Oven Options
Kleenair is the nation’s premier industrial furnace and oven manufacturer, offering a broad range of custom batch and continuous industrial furnace and oven options to meet your application needs. Our experts can produce the following types of custom industrial furnaces and ovens:
Forging Furnaces
Our custom forging furnaces provide superior temperature uniformity and usability to ensure all process temperatures are met during your forging operation.
Forging FurnacesHeat Treating Furnaces & Ovens
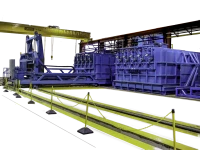
Our custom industrial heat-treating furnaces feature fully programmable controls and optional automated material handling and quenching systems for reliable heat treating.
Heat Treating Furnaces & OvensTungsten & Molybdenum Reduction Furnaces
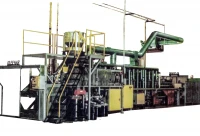
Our custom tungsten and molybdenum reduction furnaces feature state-of-the-art controls and HMIs (human-machine interfaces) for precision control of your reduction processes. With our easy-to-use control systems, programming your reduction furnace's temperature, time, and atmospheric requirements is a snap.
Tungsten & Molybdenum Reduction FurnacesTitanium & Zirconium Reduction/Distillation Furnaces
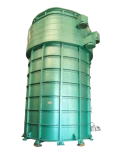
Kleenair’s custom reduction and distillation furnaces are built to meet your performance requirements and are easy to program for strict process management.
Titanium & Zirconium Reduction/Distillation FurnacesPowdered Metal Sintering/MIM Furnaces

Kleenair's sintering furnaces can reach up to 3,300°F (1,816°C). Parts can be sintered into the final part shape or in a raw shape that requires additional machining or finishing.
Sintering/MIM FurnacesInvestment Casting Furnaces
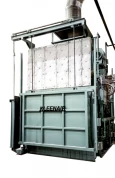
Custom investment casting furnaces from Kleenair can reach the high and consistent temperatures required to remove wax and polymers from ceramic molds. The intuitive software and custom functionality provide the user precision control of your investment casting operation's temperature, duration, and processing atmosphere.
Investment Casting FurnacesQuenching Systems
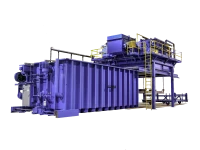
Kleenair can provide a custom quenching system seamlessly integrated with your industrial furnace, with customized controls and automated material handling technology for fast and efficient quench processing.
Quenching SystemsAutomatic Material Handling Systems & Solutions
As your process requires, Kleenair Products can integrate automated material handling systems into your furnace or oven. We can develop custom-designed robotic or other types manipulators tailored to your unique process requirements or provide “standard” solutions from Siemens, Fanuc, and other industry-leading robotics OEMs.
Advantages of Material Handling Systems
Automatic material handling systems provide benefits that cannot be matched by manual systems. Some of the most significant advantages of robotic material handling systems include:
- Increased uptime
- High levels of consistency
- Faster production times
- Decreased cycle times
Why Choose Kleenair Products Co. for your Custom Industrial Furnace & Oven Needs?
With over 50 years of experience designing, engineering, and manufacturing custom industrial furnaces and ovens, Kleenair can produce a custom furnace or oven based on your exact needs and specifications. Some of the advantages of working with Kleenair for your custom-built industrial furnace and oven needs includes:
- Unrivaled Experience & Expertise
- Unique Custom Options
- Premium Quality Materials
- Ongoing Support Throughout the Life of the Furnace or Oven
Contact Kleenair Products Co. for Custom Industrial Furnaces & Ovens Today
Turn to Kleenair for the design, engineering, manufacturing, and installation of a custom industrial furnace or oven that meets your application and performance requirements. To speak with someone directly, call 800-275-5152, request a quote, or contact us to discuss your project today.